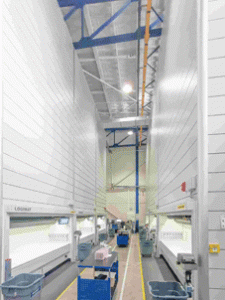
In order to further optimize material provision for Oerlikon Neumag and Oerlikon Nonwoven business units and to strengthen internal processes at the German site in Neumünster, Germany, the Manmade Fibers segment of the Swiss Oerlikon Group decided last year to invest in a state-of-the-art logistics center with a new lift center.
The center has already been fully operational for a few weeks. This is extremely helpful for speeding up the processing of the numerous orders for meltblown systems for manufacturing high-quality nonwovens for protective masks and apparel that Oerlikon Nonwoven received over the past months.
Investing in a new Oerlikon Neumag and Oerlikon Nonwoven logistics center is paying dividends: the processing speed when manufacturing new systems – very much to the benefit of customers – considerably improved in the first week after the center started operating, not least as a result of the optimized processes and material handling. After 25 years, the time had finally come to break new ground and to better equip themselves for the future requirements of the markets. The paternoster storage facility not only needed to have regular repairs carried out due to its age, it was also too small for the projects increasingly being carried out today. The only 90 square meters were capable of storing around 12,000 parts. In contrast, the new logistics center offers more than 250 square meters of storage space for in excess of 25,000 parts. As a result, this now also houses all small parts, which used to be stored in the high-rack facility due to lack of space.
New Hardware and Software
Coinciding with the opening of the new logistics center, Oerlikon also introduced new digital processes that also help cope with the increasing production volumes. Consistently maintained master data and photos for all parts ensure safe, paper-free storage and handling of materials. In order to minimize mistakes, a laser pointer now indicates from which or to which space the goods are moved. Furthermore, a photo of the material, sorted to type, is displayed on the screen. The digitalization of warehousing facilities secures the pick and put-away process so that checking material numbers becomes superfluous when removing items from the warehouse.